Converting Process Solutions
Contents
Spooling Options
Spooling, or Traverse Winding a product is becoming increasingly common. Although spooling still lends itself to narrow width slitting
production, it is no longer an option to spool simply because the product is too narrow to wind in the conventional Pancake/Planetary Wound
format. Indeed, it is more likely to be the end users demand for production efficiency that dictates that the necessity for his product to be supplied in a spooled format.
In this format, your customer can get production runs of at least 10 times that of planetary rewound reels. In many cases, twenty times or more length is possible.
We have a range of multi-station spooling/traverse winding systems, some of which have been developed specifically for the following industries:
• | Flexible packaging materials (adhesive or non-adhesive) |
• | Security holograms. |
• | High and low density foams (adhesive or non-adhesive). |
• | Nonwoven's. |
• | Tear tape. |
Utilising existing slitting equipment
If it is the case that you are already slitting and rewinding and you have only a small spooling demand we have a package that can attach to your existing
equipment. Instead of winding on to your rewind mandrels, the tapes are diverted out of the slitter and to the spooling heads.
For the converters who have only a small initial demand we have developed a 'Starter Pack System'. This is a miniature version of our multi-station flexible
packaging style system, which allows for easy expansion so you can start small and grow with your demand.
|
|
 |
Multi-station Spooling Machine |
|
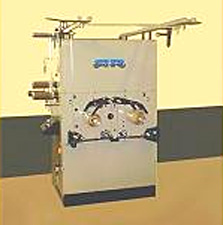 |
Starter Pack System |
|
Waste Trim Spooling Units
These can be applied to any number of processes:
• | Slitter rewinds. |
• | Printing presses. |
• | Coating and laminating lines. |
• | Film extrusion lines. |
Why use trim spooling instead of conventional vacuum extraction?
• | Managing open adhesive products that stick to extraction nozzles. |
• | Low dust contamination (no high speed airflow circulating dust). |
• | High density waste management. |
• | Better management for recycling. |
• | Coreless rewind option. |
|
|
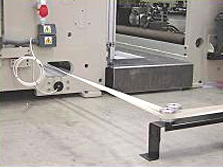 |
Waste trim |
|
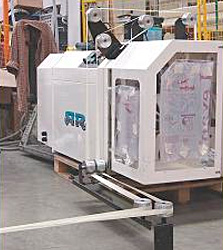 |
High-speed dual trim spool unit. Rated to 600m/min. |
|
Rewind Salvage - Doctor Machine & Inspection Options
This equipment was originally designed to correct the winding of damaged (dished/telescoped and core damaged) secondary slit rolls of
flexible packaging materials. It has subsequently been developed to cover other areas of Salvage and correction, such as:
• | Correction of wind direction. |
• | Inspection of roll. |
• | Doctoring of the rolls. |
• | Slitting or edge trimming of mini-rolls. |
• | Change of core size. |
This cantilevered, flange located, unwind mandrel is connected to a precision high speed guiding assembly. The pneumatically
expanding mandrel is quick to load/unload. Different size mandrels are also available and are quickly interchangeable.
The cantilevered, flange located, rewind mandrel winds in combination with a rubber covered lay-on roller, which can have its
contact force adjusted to compensate for diameter and speed. The rewind is capable of working in constant torque or constant
tension modes, with a fully adjustable taper tension facility, making it an ideal winder for a very large range of materials.
This range of winders starts with single direction small roller specifications. We cover all industry standard sizes up to 1270 mm
diameter reels. With accessories such as:
• | Fully reversible drive system, with selectable wind direction. |
• | Integral load/unload on larger models. |
• | Inspection with splicing table. |
• | Slitting assembly. |
|
|
|
Whatever your winding and salvage requirements are, we will have the combination for your solution.